Are you considering Industry 4.0?
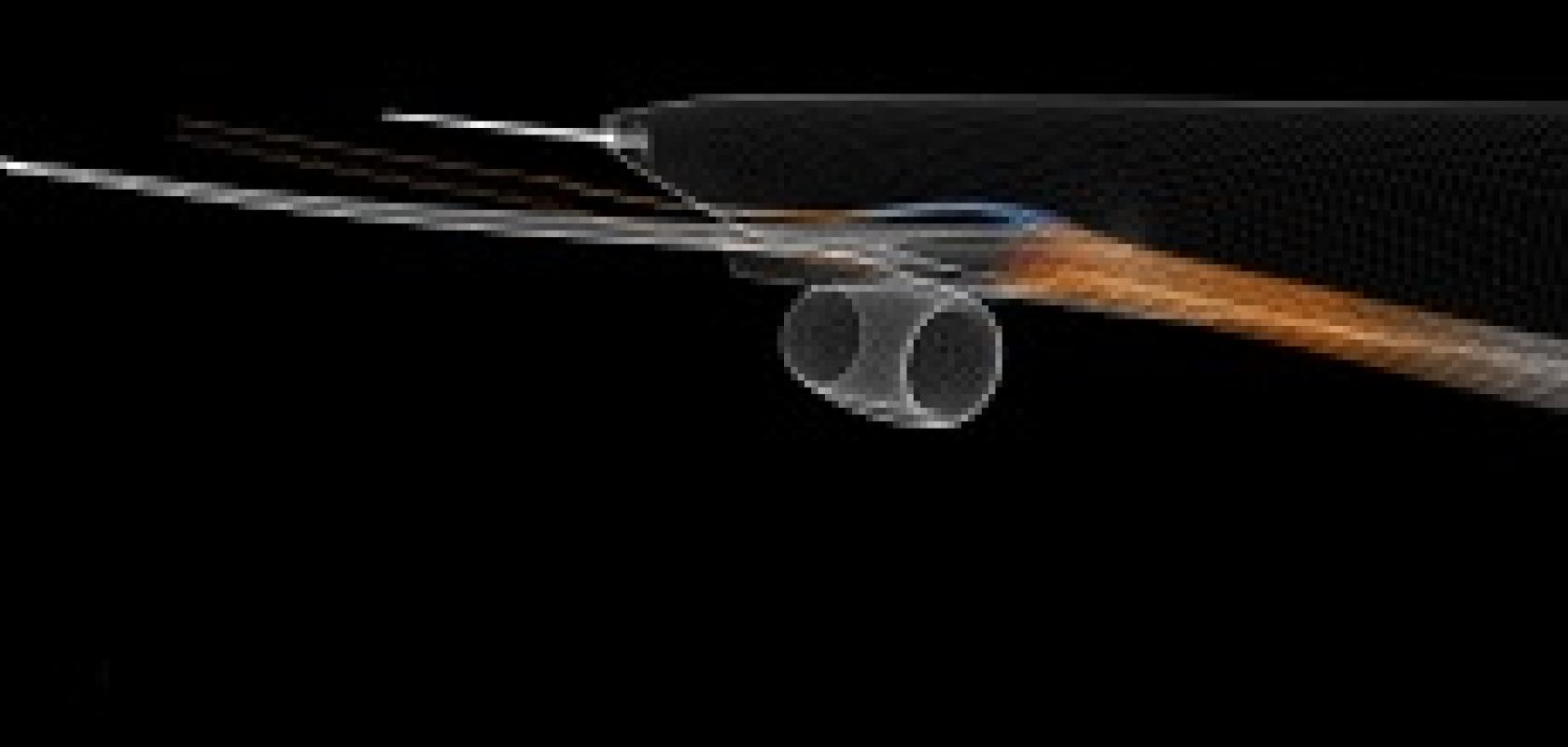
Sanjay Khetia, Chief Technology Officer at the Centre for Modelling and Simulation (CFMS), talks about Industry 4.0, and the use of modelling and simulation to explore its possibilities.
Industry 4.0 is predicted to completely revolutionise the design and manufacture of every product by combining cutting-edge connected technologies with the established manufacturing processes. Its goal is to ultimately achieve significant cost savings without compromising on product quality.
The basic premise of Industry 4.0 is to take every manufacturing process and import it into one holistic system where the workflow, maintenance and management of every machine, process or even a factory’s entire shop floor can be monitored and controlled from one or number of remote or collocated hubs.
Connected technologies, such as the Internet of Things (IoT) and cloud computing, are incorporated into a manufacturing system to produce a hybrid cyber-physical production system - predicted to produce exabytes of raw data. Within the manufacturing industry, it is safe to say that these systems will not just increase in size, but also in complexity.
It is envisaged that with Industry 4.0, such software-enhanced machinery not only has the computing power of typical IoT objects, but also includes embedded sensors and actuators to enable data capture at every stage of the design and manufacturing process. This, in turn, allows the system to self-diagnose and make decisions based on its current state - creating “smarter” design and manufacturing.
The Benefits
Industry 4.0 attempts to realise manufacturing’s Holy Grail: the desire to increase quality, but reduce costs. It achieves this by allowing manufacturers to take a proactive, as opposed to reactive approach, and to increase profitability and productivity. It enables more informed decisions based on real data, and in real time, to boost capacity and quality.
It is envisaged that there will be a substantial reduction in human error leading to improved production quality. This allows human intervention to be focused on activities such as optimising the industrialisation processes, as opposed to altering machine diagnostics and parameters.
Creating the opportunity for cost effective mass customisation, Industry 4.0 allows one manufacturing process to form the foundation for multiple bespoke designs. With no requirement or impact to redesign the equipment or processes if a customer wants a different design, the premise of a single system simplifies the manufacturing process to the point where a factory can react to influxes in demand with ease and at a low cost.
This approach has already seen success in the consumer world, where large online retailers use tracking software to allow the customer to determine the status of an order and location. Information is presented to the customer real-time, removing the need to make numerous phone calls to find the information, reducing customer time spent on querying, while delivering cost savings to the retailer.
The ability to continually evolve and optimise the digital system to the point where the best product is produced at the lowest cost, should undoubtedly benefit both the consumer and the manufacturer. Industry 4.0 is based upon this philosophy. Its goal is to build a digital or connected system that communicates, automates the manufacturing process, reports failures, reports interesting metrics for improvement and deploys human or machine fixes.
Current State of Play
The development of methods, technologies and machinery for Industry 4.0 is still in its infancy as the cost of change is a barrier to widespread adoption across the manufacturing sector.
While a small number of manufacturers are working towards a fully integrated environment, the majority of those interested in such technologies are retrofitting Industry 4.0 solutions into their existing facilities to optimise their processes. Although these are small steps, they demonstrate progression towards the end goal and vision of achieving an automated environment and evidence of the utilisation and belief of Industry 4.0
A challenge for Industry 4.0 is to, effectively, get disparate pieces of machinery and processes to interoperate with one another using a common language. The development of such a solution requires a standard. In line with its vision to transform American manufacturing and usher in the digital revolution within the US, the Digital Manufacturing and Design Innovation Institute (DMDI) has created such a standard. The industry step change required to address adoption is the consideration that one size does not fit all within the manufacturing space, but rather a combination of standards for different levels, architectures and systems would significantly aid Industry 4.0 development.
Future 4.0
Despite its holistic nature, the future of Industry 4.0 is not based on a single solution. The range of technologies and methodologies required to deliver a viable industrial solution needs to be demystified and explored without risk and significant investment. One such way of exploring the possibilities of Industry 4.0 is through the use of Modelling and Simulation. By creating a virtual system or digital prototype, manufacturers will have the opportunity to test configurations and visualise potential outcomes and return on investment. Against the backdrop of continuous improvement, these virtual systems could provide support for through life activities, for example to plan maintenance work through testing different configurations which should result in reducing downtime and maximising any activities.
Although only small steps are visible to date within industry, further interest and adoption within the design and manufacturing sector, could be the tipping point for the Fourth Industrial Revolution. There is little doubt that Industry 4.0 is complex, the benefits of digitising design and manufacturing are clear, though the path to achieving the vision propelling Industry 4.0 will be different for every organisation. The Centre for Modelling & Simulation (CFMS) is leading the Future Engineering Systems project, which is a £4.22m consortium that aims to develop and demonstrate a prototype infrastructure to fully integrate engineering data sources within the process lifecycle management (PLM) tool chain. Resulting in the creation of a prototype or connected system at CFMS, this project has the potential to demonstrate the tangible benefits of Industry 4.0.